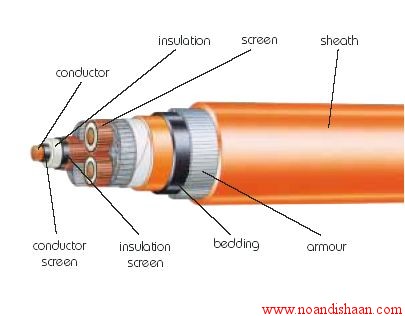
کابلها نقشی مهم در فرایند انتقال انرژی الکتریکی دارند و با توجه به ویژگیهای عملکردی خاص از دیرباز به عنوان یک گزینه منحصر به فرد، در شبکه های داخلی کارخانجات، وظیفه تامین برق مورد ماشین آلات و دستگاههای موجود را بر عهده دارند. امروزه با توجه به گسترش افقی و عمودی شهرها، تأمین برق مطمئن و با کیفیت برای مشترکین، مستلزم ایجاد پستهای انتقال، فوق توزیع و توزیع متعدد در داخل محدوده شهرها و نزدیک به مراکز ثقل بار و احداث خطوط انتقال، فوق توزیع، فشار متوسط و فشار ضعیف به عنوان خطوط تغذیه و تامین برق میباشد. احداث خطوط هوایی، مستلزم آزاد نگهداشتن قسمتی از دو سمت مسیر اطراف خط تحت عنوان حریم خط می باشد که در این مجدوده با محدودیتهایی مانند ممنوعیت ساخت و ساز مواجه هستیم. عرض این مسیر آزاد با افزایش سطح ولتاژ افزایش مییابد. با توجه به کمبود و ارزش بالای زمینهای داخل شهرها (به ویزه در شهرهای بزرگ و پر جمعیت) و نیاز به سرمایهگذاری کلان جهت تملک زمینهای مورد نیاز، امکان انتقال انرژی الکتریکی مورد نیاز مشترکین بصورت هوایی، روز به روز کاهش می یابد، به علاوه، به سبب اینکه خطوط هوایی، اغلب با هادیهای بدون روکش (هادی لخت) طراحی و احداث شده و در معرض عوامل متغیر محیطی قرار دارند، لذا از قابلیت اطمینان خیلی بالایی برخوردار نمیباشند. در چنین شرایطی استفاده از کابلهای قدرت به عنوان یک آلترناتیو جدی مطرح میباشد. عمده مزیت کابلها نسبت به خطوط هوایی قابلیت اطمینان بالاتر میباشد بطوریکه به دلیل دفن مستقیم کابل در خاک یا نصب در تونلهای زیر زمینی، با عوامل متغیر محیطی در ارتباط نبوده و خطرات ناشی از بروز حوادث به میزان قابل توجهی کاهش مییابد. نقاط ضعف عمده سیستمهای کابلی در مقایسه با خطوط هوایی عبارتند از:
هزینه اجرایی بالاتر (هرچه سطح ولتاژ افزایش یابد اختلاف هزینه قابل ملاحظه تر می شود)
مشکل و زمانبر بودن امکان عیب یابی و نیاز به تجهیزات عیب یاب ویژه در صورت بروز عیب
مشکل و زمانبر بودن و نیاز به تجهیزات و تخصصهای خاص جهت انشعاب گیری
نیاز به تجهیزات و تخصصهای خاص جهت ترمیم نقاط آسیب دیده و …
البته با اتخاذ تمهیداتی از قبیل ایجاد تونلهای مشترک خدمات شهری، هزینههای نصب سرشکن شده و هزینه اجرایی به ازاء هر خط کابلی کاهش مییابد. مشاهده می گردد علیرغم برتریهای متعدد خط هوایی در مقایسه با کابل به سبب مسایل مربوط به حریم خطوط، استفاده از کابلها توجیه اقتصادی پیدا می کند. در ادامه ضمن طبقه بندی کابلهای قدرت، فرایند تولید کابلهای فشار قوی که به عنوان جدی ترین گزینه انتقال انرزی الکتریکی در سطوح ولتاژ انتقال و فوق توزیع در سالهای پیش رو میباشد، آورده میشود:
انواع کابلهای قدرت:
۱- کابلهای فشار ضعیف
۲- کابلهای فشار متوسط
۳-کابلهای فشار قوی
مراحل ساخت کابل فشار قوی:
الف: تک رشته بدون زره:
۱- نازک کردن مفتول به قطر دلخواه با استفاده از دستگاه کشش و قالبهای الماسه
۲- آنیل کردن سیم نازک شده با استفاده از دستگاه آنیلر
۳- تابیدن رشتههای نازک شده با استفاده از دستگاه استرندر و تابیدن نوار نیمههادی با استفاده ازTaper
۴- اکسترود کردن همزمان لایههای نیمههادی داخلی (هادی) عایق پلی اتیلن کراسلینک و لایه نیمههادی داخلی با استفاده از دستگاهCV (CCV , VCV) و انجام عملیات کراسلینک کردن پلی اتیلن با استفاده از روش پر اکسید و بخار آب (داخل لوله ولکانیزاسیون)
۵- تابیدن نوار نیمههادی بیرونی و تابیدن رشتههای شیلد الکترو استاتیکی و نوار پلی استر با استفاده از دستگاه استرندر
۶- اکسترود کردن روکشPVC با استفاده از دستگاه اکسترودر و حک کردن مارک (استاندارد ساخت، ولتاژ، تعداد رشتهها، سطح مقطع و متراژ) بر روی کابل
۷- ریوایند، اندود کردن سطح روکش بهوسیله کربن و پیچیدن کابل روی قرقره با متراژ مناسب
۸- تستهای الکتریکی نهایی (تست ولتاژ و تست تخلیه جزئی (Partial Discharge)بر اساس استاندارد IEC 60840)
۹- سرکابل زنی و بستهبندی
۱۰- حمل به انبار
۱۱- بارگیری
ب: تک رشته زرهدار:
ب-۱: زره مفتولی:
۱- نازک کردن مفتول به قطر دلخواه با استفاده از دستگاه کشش و قالبهای الماسه
۲- آنیل کردن سیم نازک شده با استفاده از دستگاه آنیلر
۳- تابیدن رشتههای نازک شده با استفاده از دستگاه استرندر و تابیدن نوار نیمههادی با استفاده ازTaper
۴- اکسترود کردن همزمان لایههای نیمههادی داخلی (هادی) عایق پلی اتیلن کراسلینک و لایه نیمههادی داخلی با استفاده از دستگاهCV (CCV , VCV) و انجام عملیات کراسلینک کردن پلی اتیلن با استفاده از روش پر اکسید و بخار آب (داخل لوله ولکانیزاسیون)
۵- تابیدن نوار نیمههادی بیرونی و تابیدن رشتههای شیلد الکترو استاتیکی و نوار پلی استر با استفاده از دستگاه استرندر
۶- اکسترود کردن لایه بدینگ(BEDING) با استفاده از دستگاه اکسترودر
۷- تابیدن مفتولهای آلومینیوم بر روی کابل توسط دستگاه استرندر و نوار پیچی
۸- اکسترود کردن روکش PVCبا استفاده از دستگاه اکسترودر و حک کردن مارک (استاندارد ساخت، ولتاژ، تعداد رشتهها، سطح مقطع و متراژ) بر روی کابل
۹- ریوایند، اندود کردن سطح روکش بهوسیله کربن و پیچیدن کابل روی قرقره با متراژ مناسب
۱۰- تستهای الکتریکی نهایی (تست ولتاژ و تست تخلیه جزئی (Partial Discharge) بر اساس استاندارد IEC 60840)
۱۱- سرکابل زنی و بستهبندی
۱۲- حمل به انبار
۱۳- بارگیری
ب: تک رشته زرهدار:
ب-۲: زره نواری:
۱- نازک کردن مفتول به قطر دلخواه با استفاده از دستگاه کشش و قالبهای الماسه
۲- آنیل کردن سیم نازک شده با استفاده از دستگاه آنیلر
۳- تابیدن رشتههای نازک شده با استفاده از دستگاه استرندر و تابیدن نوار نیمههادی با استفاده از Taper
۴- اکسترود کردن همزمان لایههای نیمههادی داخلی (هادی) عایق پلی اتیلن کراسلینک و لایه نیمههادی داخلی با استفاده از دستگاهCV (CCV , VCV) و انجام عملیات کراسلینک کردن پلی اتیلن با استفاده از روش پر اکسید و بخار آب (داخل لوله ولکانیزاسیون)
۵- تابیدن نوار نیمههادی بیرونی و تابیدن رشتههای شیلد الکترو استاتیکی و نوار پلی استر با استفاده از دستگاه استرندر
۶- اکسترود کردن لایه بدینگ(BEDING) با استفاده از دستگاه اکسترودر
۷- پیچیدن نوار آلومینیوم بر روی کابل توسط دستگاهTAPER
۸- اکسترود کردن روکشPVC با استفاده از دستگاه اکسترودر و حک کردن مارک (استاندارد ساخت، ولتاژ، تعداد رشتهها، سطح مقطع و متراژ) بر روی کابل
۹- ریوایند، اندود کردن سطح روکش بهوسیله کربن و پیچیدن کابل روی قرقره با متراژ مناسب
۱۰- تستهای الکتریکی نهایی(تست ولتاژ و تست تخلیه جزئی (Partial Discharge) بر اساس استاندارد IEC 60840)
۱۱- سرکابل زنی و بستهبندی
۱۲- حمل به انبار
۱۳- بارگیری
۱- هادی
۲- لایه نیمه هادی داخلی (هادی)اکسترود شده
۳- لایه عایق اکسترود شده
۴-لایه نیمه هادی بیرونی (عایق) اکسترود شده
۵- نوار نیمه هادی بیرونی
۶- شیلد الکترو استاتیکی متحد المرکز
۷- لایه بدینگ
۸- زره نواری
۹- غلاف (روکش) اکسترود شده و آغشته به گرافیت
[vc_message message_box_color=”blue” icon_fontawesome=”fa fa-link”]منبع: آموزشکده ابن حسام بیرجند[/vc_message]