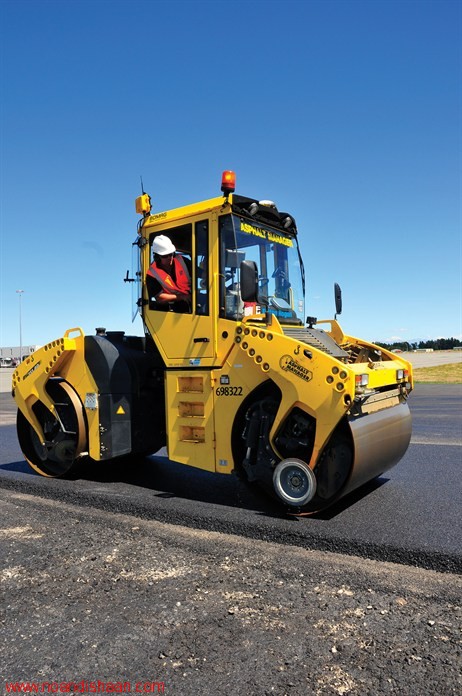
۱- کلیات
۲- معیار تراکم
۳- آزمایشهای تراکم
۴- تعداد غلتکهای مورد نیاز
۵- روش غلتکزنی
۶- غلتکزنی درزهای عرضی
۷- غلتکزنی درزهای طولی
۸- غلتکزنی اولیه
۹- غلتکزنی ثانویه
۱۰- غلتکزنی نهایی
۱۱- سطوح غیر قابل دسترسی برای غلتکها
۱۲- تصحیح ناهمواریهای سطح
۱۳- کنترل ترافیک
۱۴- عوامل موثر در تراکم
۱۵- ترک ناشی از تراکم
۱- کلیات
تراکم نقش مهمی در کیفیت ساخت راه و به خصوص لایه های روسازی آن دارد. تا چندی قبل، تراکم بعنوان بخش مهمی از فرآیند ساخت تلقی نمی شد ولی با تحلیل های اقتصادی جامع در مورد روسازی ها، به وضوح مشخص شده است که طول عمر مورد نظر و هزینه های نگهداری لایه های گرانقیمت آسفالت در حد زیادی به ظرفیت باربری آن، یعنی در واقع به تراکم لایه های آن بستگی دارد.
لایه های آسفالتی، بعد از پخش، باید به منظور تحمل بارها، توزیع بهتر فشارهای وارده و نیز ایجاد یک سطح صاف و هموار، متراکم شوند. در نتیجه تراکم، لایه ها به هم می چسبند تا یک سازه متراکم و بدون درز تشکیل شود و در مقابل نیروهای برشی حاصل از ترافیک بهتر عمل کنند. با کم شدن فضای خالی در آسفالت، مقاومت آن در برابر شرایط آب و هوایی و نیز فرسایش بیشتر شده و باعث دوام بیشتر آسفالت خواهد شد و با کاهش ناهمواری سطح، ایمنی ترافیک و راحتی رانندگی بیشتر میشود و بار ضربهای ترافیک برروی آسفالت کم می گردد.
با توجه به موارد فوق الذکر، ضروری است که در تراکم آسفالت بیشتر دقت شود تا نتیجه مطلوب حاصل گردد. در راستای بهبود کیفیت تراکم مخلوط های آسفالتی توضیحاتی را به شرح زیر ضروری میداند:
اکثر مخلوطهای آسفالتی چنانچه در دماهایی که غلظت ( ویسکوزیته ) قیر مناسب باشد پخش و غلتک زنی شوند به خوبی متراکم میگردند. غلتکزنی باید بلافاصله بعد از پخش مخلوط آسفالتی در درجه حرارت مناسب شروع شود. ولی به منظور تامین کیفیت مطلوب لایه های آسفالتی، غلتکزنی باید با دقت صورت گرفته و از ایجاد زبری و ناهمواری زیاد در سطح روسازی جلوگیری کند.
بعد از پخش آسفالت، غلتکزنی درزهای طولی باید سریعاً انجام شود. غلتکزنی اولیه باید تا حد امکان سریعتر ( در درجه حرارت مناسب ) انجام شود، بدون اینکه در مخلوط ترک ایجاد شود و یا مخلوط بوسیله لاستیکهای غلتک از جای خود بلند شود. البته غلتکزنی اولیه نباید خیلی سریع شروع شود زیرا شروع زود هنگام غلتکزنی عواقبی را به شرح زیر به دنبال خواهد داشت:
– چسبیدن مصالح به جدار غلتک ( با وجود آب پاشی سطح جدار آن ).
– ظهور ترکهای عرضی در پشت جدار غلتک.
– ایجاد برآمدگی و چینخوردگی در جلوی غلتک.
غلتکزنی ثانویه باید بلافاصله بعد از غلتکزنی اولیه انجام شود و تا زمانی که دمای مخلوط به مقداری است که میتواند به چگالی ماکزیمم برسد ادامه یابد. غلتکزنی نهایی تا زمانی باید ادامه یابد که مخلوط هنوز برای برطرف کردن اثر غلتک ( ناهمواری ) حالت شکلپذیری دارند. موضوع زیر بعنوان یک خطمشی پیشنهاد می شود:
درزهای طولی و لبه ها بلافاصله بعد از پخش، غلتکزنی شوند. غلتکزنی اولیه حدود ۶۰ متر بعد از فینیشر و غلتکزنی ثانویه ۶۰ متر و یا کمتر بعد از غلتکزنی اولیه و غلتکزنی نهایی تا حد امکان سریعتر و بعد از غلتکزنی ثانویه انجام شود.
اگر چگالی مورد نظر در هنگام اجرا بدست نیاید، ترافیک بعدی، روسازی را تحکیم میدهد که این عمل باعث نشست در زیر چرخهای وسایل نقلیه میشود. برای رسیدن به چگالی مورد نظر و یک سطح قابل قبول، توصیه میشود که از غلتک چرخ لاستیکی با فشار تماس بالا همراه با غلتک چرخ فولادی استفاده شود.
غلتک های ویبره نیز در این کار مفید و با ارزش هستند و چون غلتک های ویبره ممکن است در مواردی موج ایجاد نماید لذا استفاده از غلتک های لاستیکی در مراحل نهایی غلتکزنی میتواند نارسایی مذکور را برطرف نماید.
نام فایل: روش تراکم آسفالت
مشاهده کامل مطلب: لینک به تالار گفتگو